Servo punch industry
The servo punch press uses the servo motor as the direct power source, and converts the driving force generated by the motor into the linear motion of the slider through the screw, crank connecting rod, toggle rod, etc. The characteristics of programmable control of the servo motor are used to perfectly control the movement form of the slider to meet the needs of diverse stamping processing and intelligence. With the advantages of controllable slider speed, easy forming of difficult-to-form materials, energy saving, environmental protection, multi-purpose of one machine and intelligence, the servo motor is currently recognized as the third generation of punch and the mainstream trend in the development of the stamping industry.
Scheme characteristics and advantages
1. Energy saving and environmental protection
3. One machine for multiple purposes
2. Intelligent processing of various molding curves
Scheme configuration network
Cases
This case is the elevator pedal production line of 7 sets of 110t servo presses using our control system.
It was deployed in 2015 and has been in continuous production for nearly 4 years.
The elevator pedal, a product produced by the customer on site, adopts the drawing process. When it approaches the mold, it decelerates to the speed of 40SPM for pressing. When it returns, the speed reaches 80SPM, and the comprehensive speed reaches 71SPM, while the asynchronous punch at the customer’s site produces at the speed of 50SPM. By comparing, we have increased our production capacity by 42%.
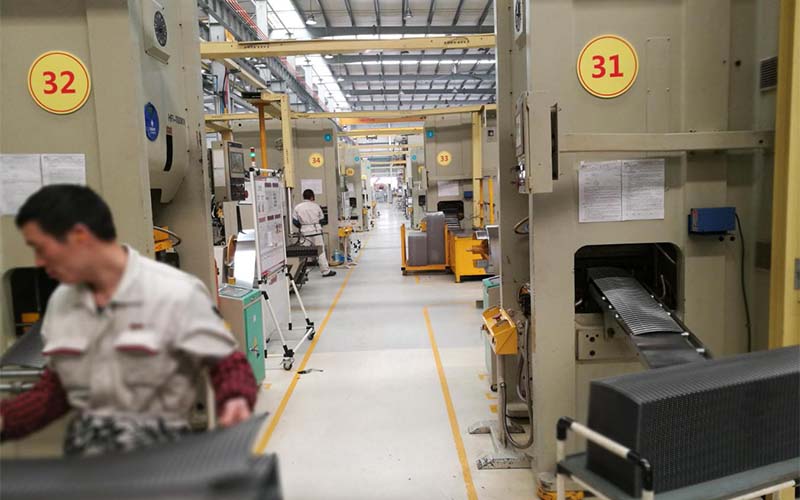
Comparison of efficiency and energy consumption between servo punch and ordinary punch:
Progressive die:
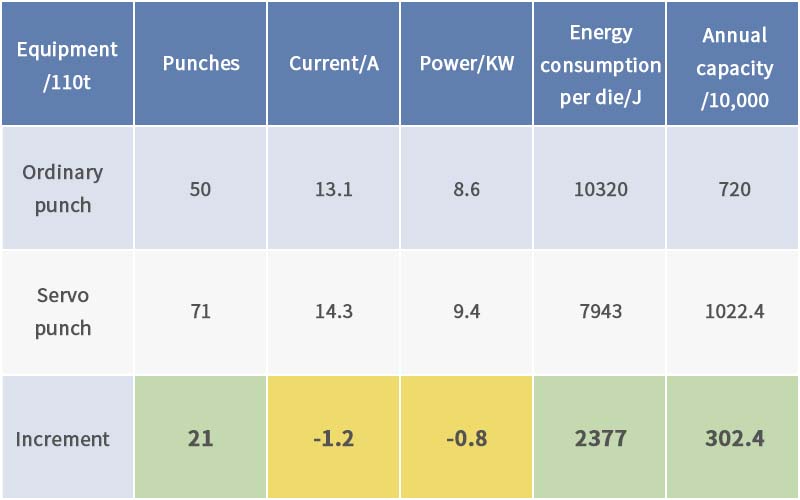
Note: the annual capacity is calculated based on 8 hours per day and 300 days per year
As can be seen from the above table, in the working mode of progressive die, the energy saving rate of servo punch is 23% and the efficiency is improved by 42% compared with that of ordinary punch. If the annual capacity is 10 million, the power saving of servo punch will be 6,604 kWh compared with that of ordinary punch. At the same time, because the stamping speed is lower, it also helps to control the noise and the service life of the die.
Single station:
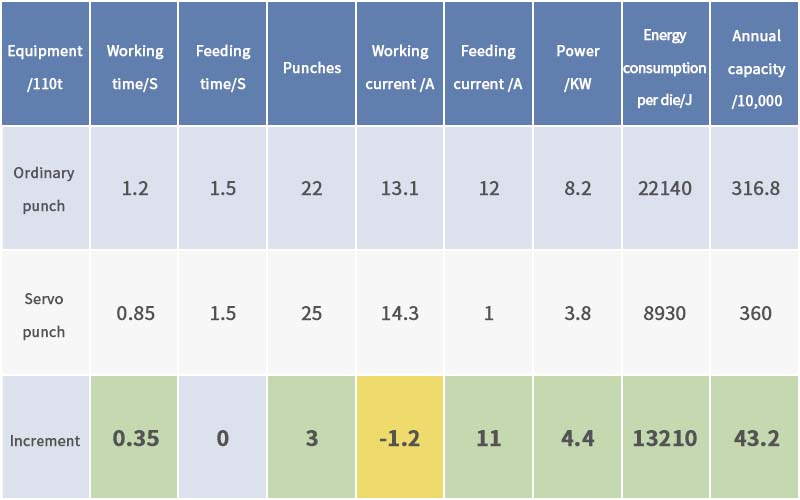
Note: the annual capacity is calculated based on 8 hours per day and 300 days per year
As can be seen from the above table, in the single station mode, the energy saving rate of the servo punch is 59.6% and the efficiency is improved by 13.6% compared with that of ordinary punch. If the annual capacity is 5 million, the power saving of the servo punch will be 18,347 kWh compared with that of ordinary punch, equivalent to that RMB 18,000 is saved per year.