Embedded motion control
The peripheral automation of the aluminum profile extruder controls the multi position, high speed and high repetition positioning accuracy of the material transfer trolley; the uncoiling, leveling and cutting control the high speed and high repetition positioning accuracy of the feeding; the tablet press controls the high repetition accuracy of the product thickness. The original ordinary axis must be replaced with servo axis control to realize technical improvement of these fields. The general plan is to upgrade the power system to a servo system drive, and replace the controller with a controller with motion control functions, and the controller must generally control the process flow and the servo axis motion, which causes high hardware costs and problems such as the software must be redeveloped.
We can provide a complete solution of embedded motion control + servo power unit. In this scheme, there is no need to replace the master controller of the original equipment, but the controller can be used as the master station of modbus communication protocol. Haitian drives the embedded motion controller as the slave station of modbus communication protocol, while the master station is responsible for the process flow and the target action of preset servo axis, and the slave station is responsible for the real-time control of servo axis action. In this way, the embedded motion controller + Haitian servo complete the servo updating and upgrading of the axis to realize the mechanical direct drive system can be of multi-axis control, synchronous control, cam control and interpolation control and that the hydraulic axis can be of closed-loop control of pressure, speed and position.
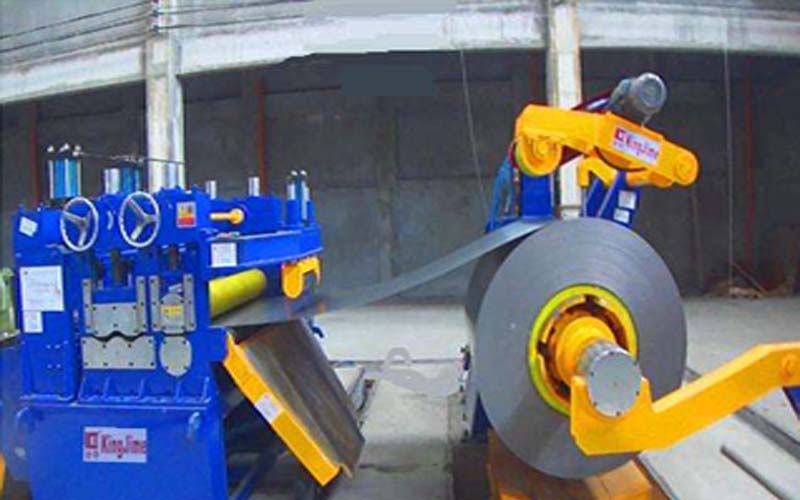
Uncoiling, leveling and cutting
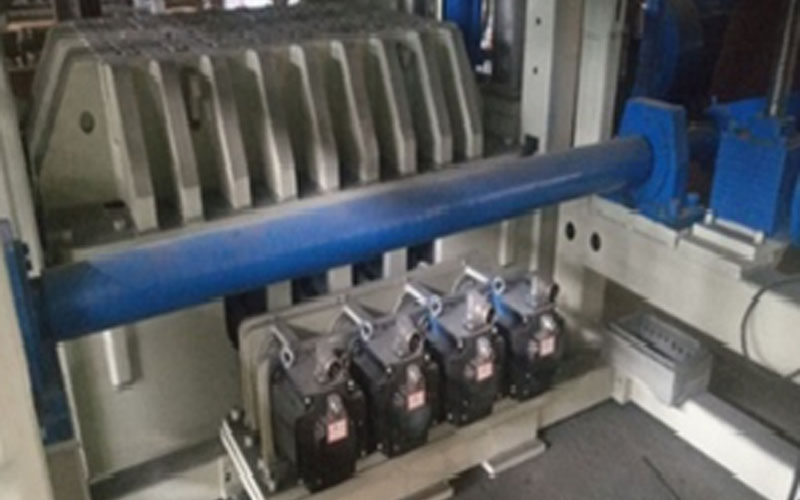
Four-axis servo vibration table
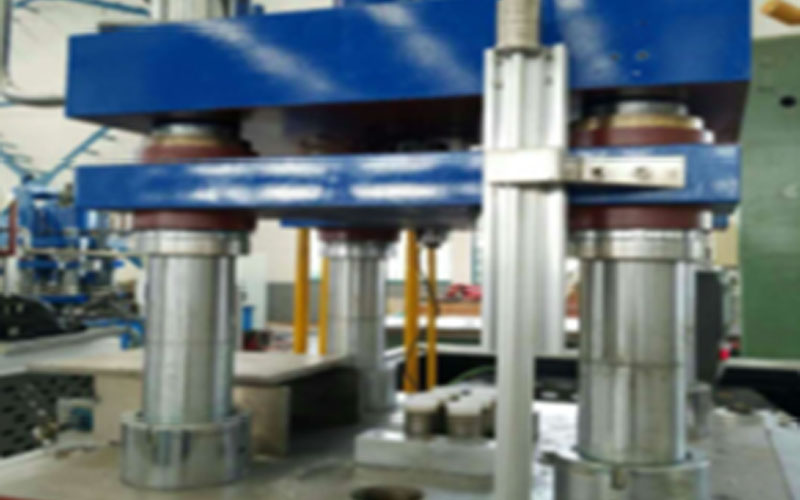
Servo tablet press
CHaracteristics and advantages
1.Easy to keep confidential and low cost
The original PLC does not need to be replaced, and the original program is slightly changed, so the manufacturer’s intellectual property of process program can be effectively kept confidential, and the cost of scheme to be implemented can be reduced.
3.Simple and reliable
The main controller and the motion controller are connected by Modbus bus, and the motion controller and the servo are connected by CANopen or EtherCAT bus, so that the production and construction of the machine are simple and the operation is safe and reliable.
2.Clear division of labor
The manufacturer’s focus is only on the production process algorithm, while the axis servo motion control algorithm should be completed by the professional Haitian drive motion controller.
Scheme configuration framework
Cases
The peripheral automation of the aluminum profile extruder performs multi-station servo control on the material transfer trolley.
Case introduction:
(Worktable) the material transfer trolley is driven by servo motor, with a reduction ratio of 1:7; the mechanical device is driven by gear rack, the servo motor and decelerating mechanism are fixed on the mobile worktable, the output of the reducer drives the gear to rotate, the rack is fixed and there are rails on the mobile worktable on which steel wheels roll (ignoring the rolling friction); the gear moves 0.6m per rotation of the worktable, and the worktable is less than or equal to 2000kg.
Technical requirements:
The maximum moving speed of the trolley is less than or equal to 1.5m/s; the acceleration and deceleration time is 0.5s; the repetition accuracy of position control is less than 1mm
Safety protection:
Emergency stop, left and right hard and soft limit, quickstop safety stop for bus disconnection detection and motor band-type brake control.
System configuration list:
S/N | Material name | Specification | Qty. |
1 | Servo motor | HP11804-G152A-E2PP7 | 1 |
2 | Servo driver | HI5.5KW | 1 |
3 | Braking resistor | 500W-40Ω | 1 |
4 | Motion controller | HIC-2000 | 1 |
5 | Cable | Supporting cable | 1 |
Specific scheme:
The main PLC of the equipment controls all logic actions, material transfer process sequence and material withdrawal / discharge actions of the aluminum profile extruder; the Haitian embedded motion controller of the slave station only controls the point position of the trolley servo system, and the two communicate by modbus TCP/IP protocol. The Haitian motion controller and Haitian servo are online controlled by CANopen.
The main PLC of the equipment writes the operating target parameters to the Haitian motion controller, such as the target position, operating speed, etc.;
The main PLC of the equipment writes the control word to Haitian drive motion controller to issue the start and stop commands of the specific operation actions;
Haitian drive motion controller receives specific command and controls Haitian servo to perform corresponding actions;
The PLC of the main equipment reads the current operating state parameters of Haitian motion controller and serves as the conditions for the next sequential control, such as reading the current operating speed and reading the loading position. When the state is reached, the loading process can be performed and the next start command for unloading positioning operation can be sent. For example, emergency stop can be performed immediately after the system alarm is received.